FEA based elastic-plastic analysis methodology
Background
Pressure vessels are subject to extensive design verifications to comply with international standards (ASME VIII, PD 5500, EN-13445, DNV-RP-C208). Most codes provide a simplified, linear analysis solution. However, as most codes recommend, the most accurate results, particularly for complex geometries, are achieved with non-linear elastic-plastic analyses.
PRE Technologies have developed a set of computational tools to optimise the post processing of non-linear elastic-plastic analyses of complex geometries to capture all the relevant failure modes.
In this example, the benefits of performing non-linear analyses are outlined in terms of design enhancement and performance.
Methodology
The ASME VIII design by analysis rules requires the verification of protection against 4 failure modes:
- Plastic Collapse
- Local Failure
- Buckling
- Fatigue
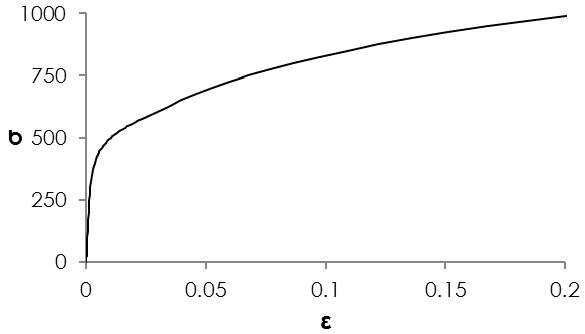
A detailed elastic-plastic material model is required to accurately represent the elastic and plastic behaviour of all components involved until failure, as shown in the figure on the right.
Based on LRFD (Load and Resistance Factor Design) methodologies, a set of load cases is developed to capture all possible scenarios. Plastic collapse and local failure are assessed for the factored design loads and service criteria are developed with the product developers to ensure functionality.
Local failure is assessed by customised tools to determine the local damage based on the limiting triaxial strain (εL), residual manufacturing strains (εcf) and equivalent plastic strains (εpeq), defined as follows:

Local damage can then be determined as the sum of the utilisations for each load case, Dε(k), and the residual manufacturing damage, Dεform.

Example
An elastic-plastic analysis was performed on a subsea valve component subjected to an internal design pressure, as shown in the next figure.
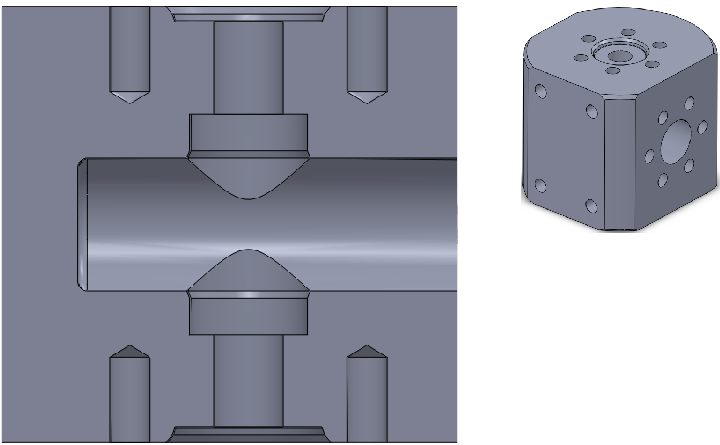
The maximum equivalent stress evaluated in the component displays an elastic behaviour up to the design pressure (as shown in the next figure), after which stresses above yield are observed.

Despite the plastic deformation sustained at the factored loads (displayed in the next figures), global criteria for the analysis are met and the local failure damage is kept well below allowable limits.
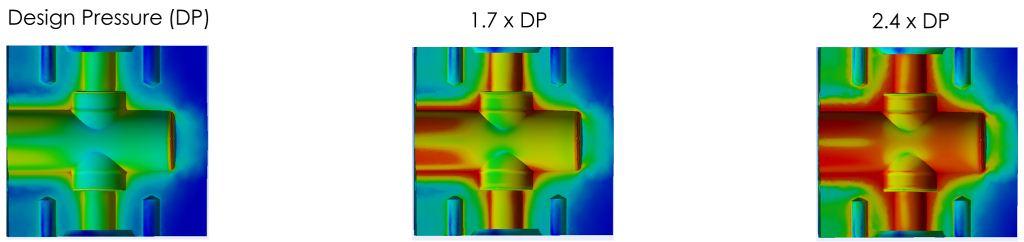
Local plastic deformation can be plotted to locate the areas where the stress values are above yielding. The next figure presents the isosurfaces for yielding stress values for the three factored pressure loading scenarios evaluated for the valve component.
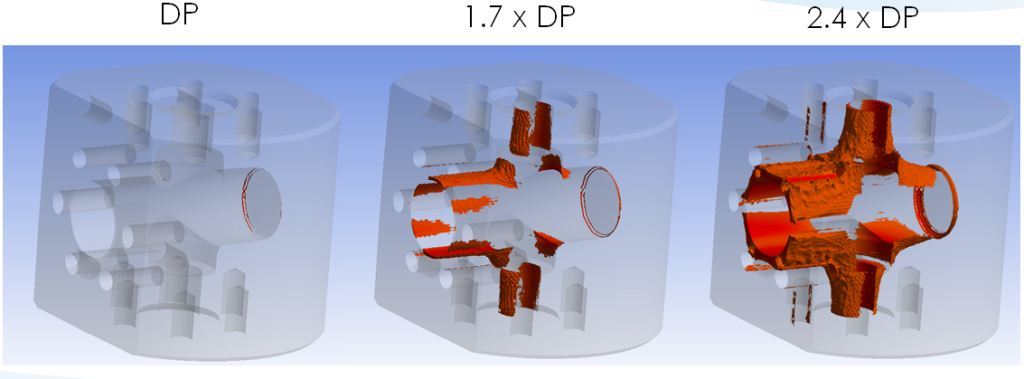
Following the same analysis procedure, a parametric study of the design pressure led to an increase in the pressure rating for the component. The next table illustrates how undertaking the more complex elastic-plastic analysis led to a 2.3 fold increase in the pressure rating for the component, 60% more than a linear elastic investigation would have yielded.
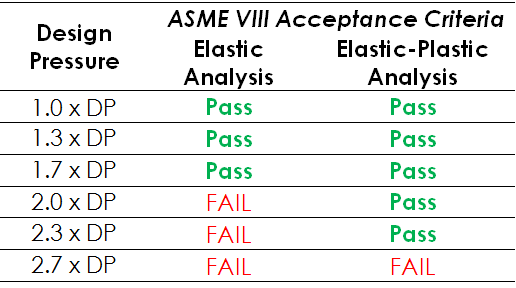
An analysis at a higher design load (40ksi) suggests that the component could sustain pressures of circa 33ksi, as presented in the next chart.
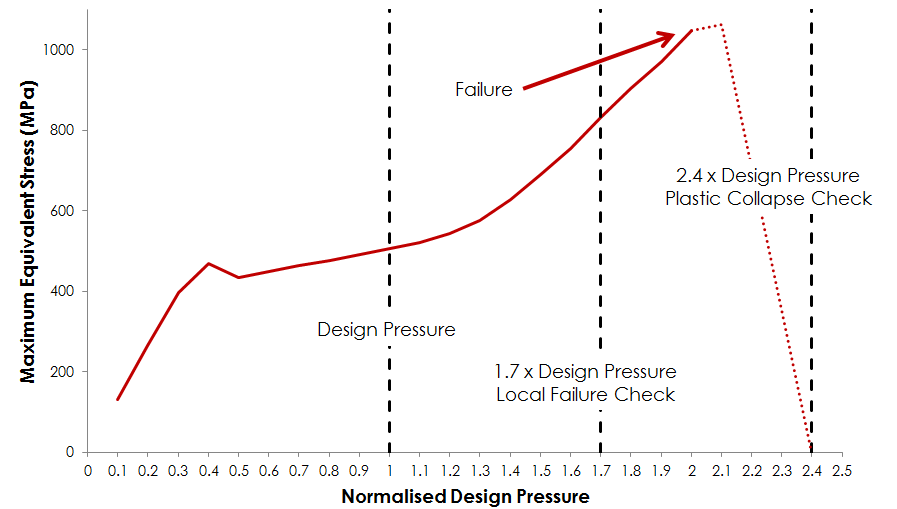
Benefits of using FEA
Elastic analysis can provide a rapid solution for a sturdy design of relatively simple geometries. For more complex components, the design optimisation and, ultimately, cost saving benefits which result from a more detailed, non-linear, elastic-plastic analysis are significant:
- In the example presented here, the pressure rating for the component was more than doubled.
- In weight critical applications, bulky components can be reduced and geometries optimised.
- In safety critical applications, the increased level of accuracy and the detailed mapping of stress concentrations and deformations can reduce testing costs by identifying critical design flaws.
- Elastic-plastic analysis can lead to acceptable and safe designs at much higher operational loads compared to linear-elastic analysis.
Please see other related articles and case studies available at the PRE Technologies website. We are constantly updating our website and aim to have a wider range of case studies in the future, so do keep in touch.
Keep your curiosity in good shape.
For more information on this or any other technical white paper, please contact us.