Pressure containing equipment
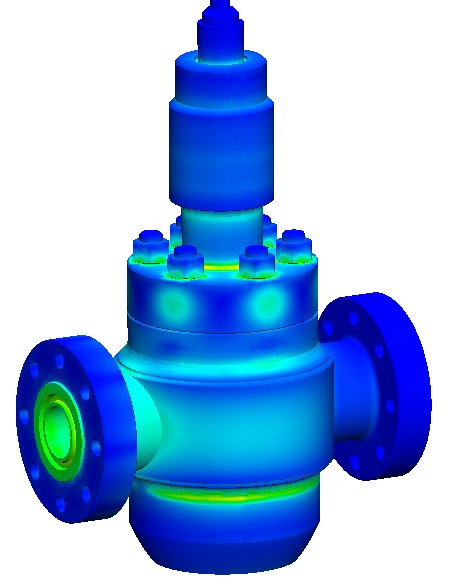
The safe operation of pressure vessels is a critical aspect of many engineering projects in sectors ranging from Oil & Gas to food production. The accumulation of pressure in unsuitable structures can be a cause for damage, significant cost and hazardous incidents. For this reason the design, fabrication and operation of pressure vessels is generally strictly regulated.
Standards assessment (ASME, API, PD5500, etc)
Following the harmonisation of national standards by the European Pressure Equipment Directive 97/23/EC (PED), there is an established procedure, which resulted in EN 13445 for the design of Unfired Pressure Vessels with pressures above 0.5 bar.
A similar set of guidelines was developed by the ASME Boiler and Pressure Vessel Code for vessels above 1 bar (15 psi). Another typical standard for the analysis of pressure vessels is BS PD 5500.
These standards are frequently referred to for the mechanical analysis of pressure containing equipment in a variety of industries. Some of the standards that refer to these methodologies include API, DNV and ISO.
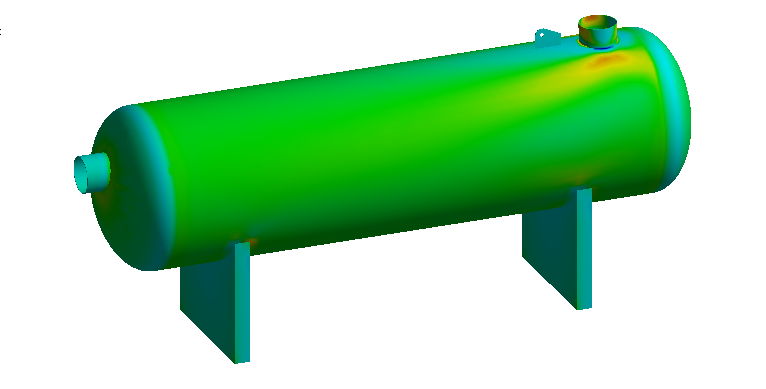
All of the standards address the effects of internal and external pressure, buckling, local failure and fatigue. Some consideration is also given to the effects of creep.
As a general rule all of these standards follow a similar structure: the design of pressure vessels can be undertaken by hand calculation, following established procedures but limiting the design in complexity and with a significant amount of conservatism. However, with the use of computational tools such as finite element analysis (FEA), it becomes possible to analyse the geometry directly with more cost effective design limits. Two solutions are generally applicable here:
- Linear elastic stress analysis with the categorisation of stresses to identify the primary stresses which must not exceed certain limits;
- Nonlinear analysis, which accounts for material plasticity, large deflections and produces a more accurate and less conservative approach to design by analysis.
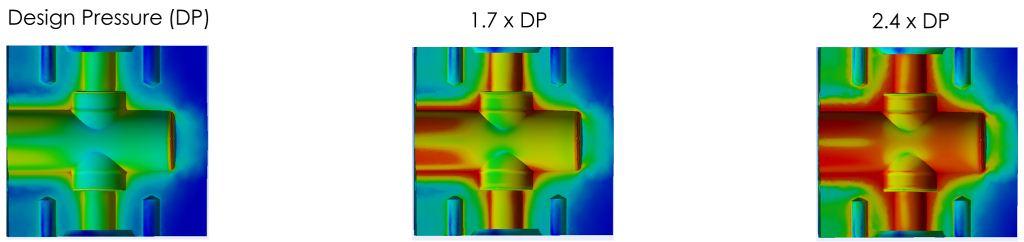
The balance of cost-effective analysis (linear) or benefits to the design (nonlinear) is a project-dependent consideration that is considered at the proposal stage. PRE Technologies has accrued extensive experience in the structural analysis of a variety of pressure equipment (valves, heat exchangers, vessels, piping, boilers and more) both by linear and nonlinear methods and following all of the above standards.
Design optimisation
In addition to structural assessment, PRE Technologies are the ideal partner for the optimisation of the design of pressure containing equipment. The use of fluid mechanics modelling using CFD has been applied for the determination of the impact of erosion, cavitation and flow optimisation as well as more traditional pressure drop determination, mixing and evaluation of recirculation zones.


Coupled fluid-structure interaction (FSI) analyses offer a holistic view of the product performance: uneven pressure distributions resulting from flow paths, acoustic or fluid induced vibrations (AIV and FIV) in piping, structurally significant thermal phenomena such as joule-thomson in subsea valves or accidental blast analysis such as steam explosions in metallurgical equipment.
For more information on other services for pressure containing systems, please go to the stress and fatigue analysis services tab or contact us here.
Our services for this sector
Standards assessment
- Standards assessment for: Valves, pressure vessels, heat exchangers, pipes, flanges, reactors, etc.
- FEA modelling following most international standards: ASME Div 2, PD 5500, API, DNV and ISO
- Studies for internal and external pressure, thermal loading, buckling, local failure, fatigue and creep
- Linear elastic stress analysis (ASME): Stress categorisation and linearization.
- Non-linear stress analysis: Material plasticity and large deflections
- Load case matrix definition based on operational and accidental loading scenarios
Design optimisation
- CFD fluid flow calculations for fluid carrying equipment
- Erosion analysis for valves, vessels and pipes
- Flow induced vibration (VIV and AIV)
- Thermal modelling and phase change studies: Joule-Thomson and cavitation modelling
- Safety assessments: Blast and fluid diffusion simulation