Heat exchanger
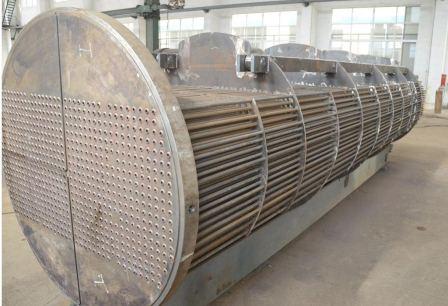

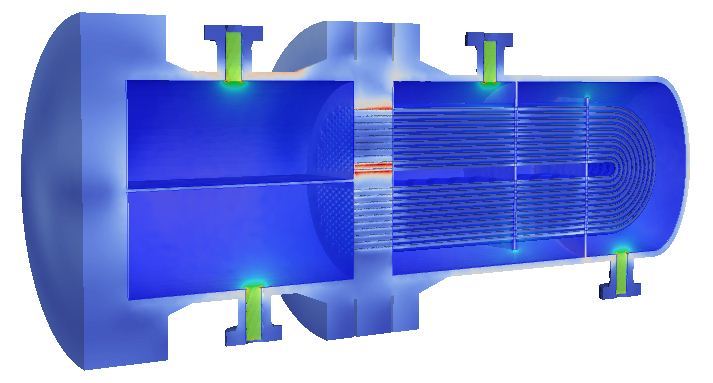
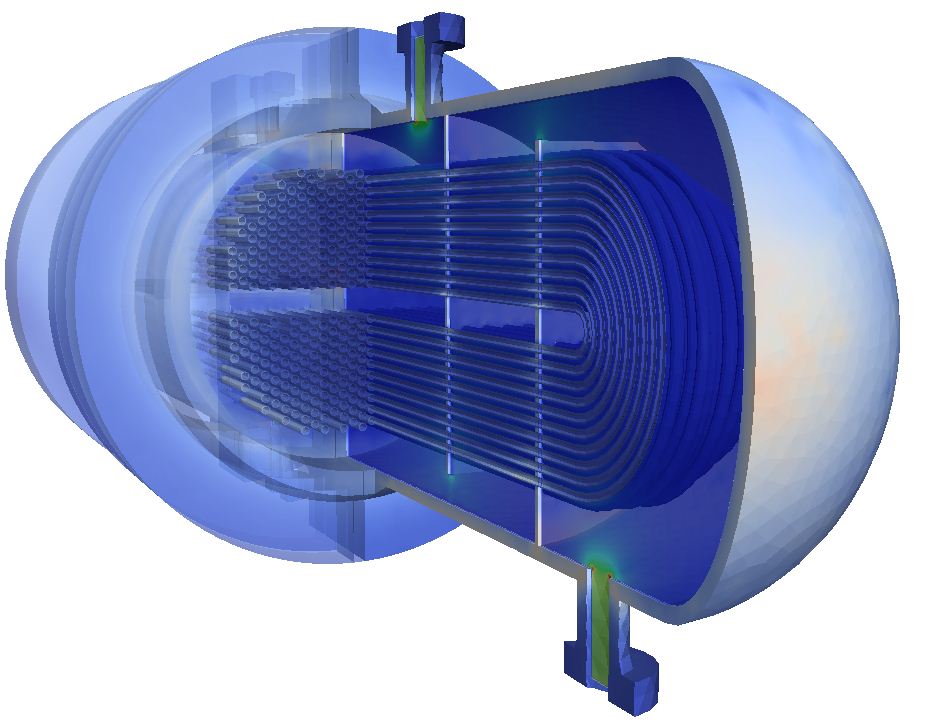
The customer
- Size: Medium-large enterprise
- Sector: Oil and gas
- Country: United Kingdom
The project
- Size: 60-75 man-hours
- Duration: 2-3 weeks
The problem
- Fatigue issues on some areas and weldings: Baffles and nozzles
- Early failure of the heat exchanger
- Fatigue useful life unknown
Proposed solution
- Stress analysis under different scenarios of temperature and pressure loads for ASME VIII-2 and PD-5500
- Fatigue analysis simulation to estimate structure's useful life (MTBF)
The simulations
- Thermal analysis to map temperatures for different cycle stages (CFD analysis)
- FEA analysis to evaluate cyclical and permanent stresses (FEA analysis)
- Fatigue calculations according to structure's expected stress map (FEA analysis)
- Optimization of the design for extended product life (FEA analysis)
Project overall results
- Increase in structure's useful life of 35%.
- Savings over £43,000 for the customer in prototyping and testing (estimate).
- Savings of more than 8 weeks in development time (estimate).
For more details about stress and fatigue calculations, please read our stress and fatigue on oil and gas sector white paper.