Plate heat exchanger
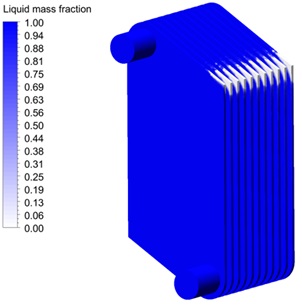



The customer
- Size: Medium-large company
- Sector: LNG operator
- Country: Germany
The Project
- Size: 80-100 man-hours
- Duration: 2-3 weeks
The Problem
- Poor flow distribution within the channels
- Chevron and channel geometry required optimisation
- Potential ice generation between the plates
Proposed solution
- Model the fluid flow for co-current and counter-current operation
- Phase change modelling for sub-zero energy carrying fluids
The simulations
- Steady-state CFD thermal simulation for the different flow scenarions (CFD analysis)
- Phase change study to obtain the areas where ice is prone to appear (CFD analysis)
Project overall results
- Optimised plates geometry for minimised stagnant zones and ice formation.
- Savings over £16,000 for the customer in prototyping and testing (estimate).
- Savings of more than 12 weeks in development time (estimate).