The Role of Computational Fluid Dynamics in Process Industries
Friday, January 17, 2014
Computational fluid dynamics has enormous potential for industry in the twenty-first century.
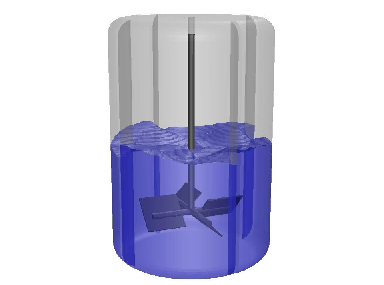
Continuum mechanics, one of our most successful physical theories, is readily applicable to the process industries. In continuum mechanics, the existence of molecules is ignored, and matter is treated as a continuous medium. The continuum hypothesis is valid, provided the equations of continuum mechanics are applied at sufficiently large length scales and time scales that the properties of individual molecules are not noticed. The mapping of the laws of mass, momentum, and energy conservation to the continuum results in field equations that describe the dynamics of the continuum. These field equations, variously known as the equations of motion, the equations of change, or simply the conservation equations, are nonlinear, partial differential equations that can be solved, in principle, when combined with the appropriate constitutive information and boundary conditions.
Analytical solutions to the conservation equations are of great interest, of course, but they can be obtained only under restricted conditions. When the equations can be rendered linear (e.g., when transport of the conserved quantities of interest is dominated by diffusion rather than convection) analytical solutions are often possible, provided the geometry of the domain and the boundary conditions are not too complicated. When the equations are nonlinear, analytical solutions are sometimes possible, again provided the boundary conditions and geometry are relatively simple. Even when the problem is dominated by diffusive transport and the geometry and boundary conditions are simple, nonlinear constitutive behavior can eliminate the possibility of analytical solution.
Consequently, numerical solution of the equations of change has been an important research topic for many decades, both in solid mechanics and in fluid mechanics. Solid mechanics is significantly simpler than fluid mechanics because of the absence of the nonlinear convection term, and the finite element method has become the standard method. In fluid mechanics, however, the finite element method is primarily used for laminar flows, and other methods, such as the finite difference and finite volume methods, are used for both laminar and turbulent flows. The recently developed lattice-Boltzmann method is also being used, primarily in academic circles. All of these methods involve the approximation of the field equations defined over a continuous domain by discrete equations associated with a finite set of discrete points within the domain and specified by the user, directly or through an automated algorithm. Regardless of the method, the numerical solution of the conservation equations for fluid flow is known as computational fluid dynamics (CFD).
CFD was initially done without automation because the need to solve these equations (e.g., in aircraft design) preceded the development of electronic computers by several decades. With the advent of electronic computers, more ambitious numerical calculations became possible. Initially, CFD codes were written for specific problems. It was natural to generalize these codes somewhat, and eventually, particularly as computational resources became more readily available, general-purpose CFD codes were developed. It was then recognized that a business could be built upon the development and licensing of these codes to industrial, academic, and government users. Today, many of the general-purpose commercial codes are quite sophisticated, cost a tiny fraction of their development cost, and are probably the mainstay of the industrial application of CFD.
Four steps are required to apply a general-purpose CFD code to an industrial problem. First, the domain must be defined. This amounts to constructing the geometry for the problem, which is typically done using a computer-assisted design (CAD)-like preprocessor. Within the preprocessor, relevant physics are defined, appropriate models are specified, boundary and initial conditions are applied, and solver parameters are specified. Because the conservation and constitutive equations must be discretized on the specified geometry, the domain discretization must be specified. This process, known as meshing or grid generation, is the second step in the application of a CFD code to an industrial problem. Meshing can be accomplished using two basic protocols: (1) structured meshing, which involves creating an assembly of regular, usually hexahedral (quadrilateral in two dimensions) elements or control volumes throughout the domain; and (2) unstructured meshing, which involves filling the geometry with control volumes, often tetrahedrons and prisms, in an irregular fashion. Unstructured mesh generators are usually simpler to use with complicated geometries and involve some degree of automation. In the third step, the equations are discretized over the specified grid, and the resulting nonlinear algebraic equations are solved. The development of solvers is still an active area of research, the goal being to improve the likelihood and rate of convergence. The fourth step, after satisfactory convergence is obtained, is to interrogate the solution to obtain the desired information. That information may be a single number extracted from the solution data set, an animation illustrating the transient macroscopic behavior of the entire flow field, or anything in between. Because the data sets can be quite large, robust tools for data set interrogation are often required.
Current Industrial Applications
CFD is routinely used today in a wide variety of disciplines and industries, including aerospace, automotive, power generation, chemical manufacturing, polymer processing, petroleum exploration, medical research, meteorology, and astrophysics. The use of CFD in the process industries has led to reductions in the cost of product and process development and optimization activities (by reducing down time), reduced the need for physical experimentation, shortened time to market, improved design reliability, increased conversions and yields, and facilitated the resolution of environmental, health, and right-to-operate issues. It follows that the economic benefit of using CFD has been substantial, although detailed economic analyses are rarely reported. A case study of the economic benefit of the application of CFD in one chemical and engineered-material company over a six-year period conservatively estimated that the application of CFD generated approximately a six-fold return on the total investment in CFD.
CFD has an enormous potential impact on industry because the solution of the equations of motion provides everything that is meaningful to know about the domain. For example, chemical engineers commonly make assumptions about the fluid mechanics in process units and piping that lead to great simplifications in the equations of motion. An agitated chemical reactor may be designed on the assumption that the material in the vessel is perfectly mixed, when, in reality, it is probably not perfectly mixed. Consequently, the fluid mechanics may limit the reaction rather than the reaction kinetics, and the design may be inadequate. CFD allows one to simulate the reactor without making any assumptions about the macroscopic flow pattern and thus to design the vessel properly the first time. Similarly, the geometrically complicated parts required for melt spinning can be designed with CFD rather than rules-of-thumb or experiments, resulting in \"right the first time\" designs.
Summary
CFD is a powerful tool for solving a wide variety of industrial problems. Commercial general-purpose codes have the potential to solve a very broad spectrum of flow problems. Current research is concentrated on overcoming the principle weaknesses of CFD, namely how it deals with turbulence and dispersed multiphase flows. Development work on solver algorithms, meshing, and user interface generation are ongoing, with the objectives of improving accuracy, reducing solution time, and increasing accessibility. In spite of the limitations of CFD, the economic value of industrial applications has been demonstrated in a variety of industries, and its value as a research tool has been accepted in many areas, such as meteorology, med-icine, and astrophysics. In industry, CFD is presently primarily in the hands of specialists, but the development of digital experts and tools to facilitate the development of digital experts may revolutionize the way industry uses CFD by providing ready access throughout the enterprise. This would result in significant gains in productivity and profitability.