FEA capabilities for composite's performance predictions
Thursday, April 24, 2014
Fibre glass composites have been around for almost 70 years. Carbon fibre came afterwards about 20 years ago and promised lighter and stronger performance. The only drawback was accurately predicting their physical properties.
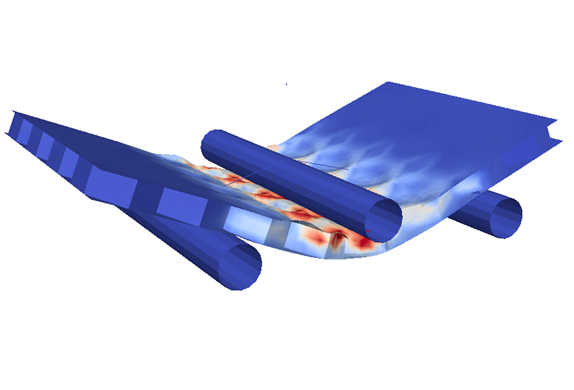
A sample analysis shows how FEA works on composites and illustrates a few recently developed features.
First, define the material properties. These are more complex for orthotropic materials such as composites. The FEA input form shows how it groups stiffness and strength properties.
Define ply layup. It is important to describe the ply stacking sequence.
Define the reference angle. Sheets of prepreg are placed on a structure either lengthwise, edgewise, or at some angle. The angle affects analysis results. Of course, a structure's fiber orientation can be complex, especially in doubly curved surfaces where fibers want to follow "great circle" routes the shortest distance between two points. FEA programs such as NEiLaminate Tools perform draping analyses to calculate the continuous variation in orientation angle.
In other cases, software can project cylindrical or spherical coordinate systems onto structure surfaces to produce a reasonable representation of ply orientation.
Represent the outer mold line. It is important to visualize the relative thickness and positions of shell structures so they can be modified as simulations reveal shortcomings.
Postprocessing. Once analysis completes, results must go to postprocessing. There is a lot of data involved in complex layup and multi-ply structures, so clear presentations needs logical approaches.
To get a feel for actual stress distributions, look at them for longitudinal, transverse, and shear directions. The combination of stresses in the X1, Y1, and XY directions contribute to the failure index.
PRE possesses a strong background in composite virtual prototyping. Contact us for more information.