FEA Aids Deepwater Horizon Failure Forensics
Friday, November 8, 2013
On the evening of April 20, 2010, Deepwater Horizon suffered a blowout while drilling in the Macondo Prospect, an area in the Gulf of Mexico 40 miles off the southeast coast of Louisiana. The platform caught fire; two days later, it sank. Many attempts were made to seal the well, but oil continued to spew into the Gulf until July 15, when a temporary cap was put in place. Relief wells then pumped concrete into the area underneath the wellhead, and the well was deemed permanently sealed in mid-September.
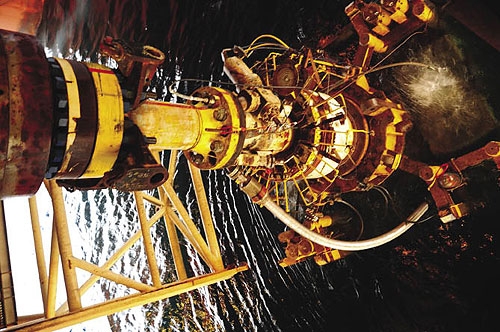
Deepwater Horizon was a semi-submersible, dynamically positioned drilling platform, or mobile offshore drilling unit (MODU). It was a huge floating oil rig, capable of adjusting position under its own power, and designed to operate in water up to 8000 feet and drill wells nearly 6 miles deep.
Blowouts occur when pressurized oil and gas flow uncontrolled up the drill pipe or riser to the rig, posing extreme risk to the people operating the rig, as well as possible damage to the environment and the platform itself. Modern rigs are equipped with blowout preventers, or BOP stacks, huge structures that sit on the sea floor directly over the wellhead. The drill pipe passes through the BOP stack, which contains a number of mechanisms—shear rams, bore rams, annular preventers, and a host of electronic and hydraulic assemblies—that are supposed to shut the well down safely in the event of a blowout.
During the initial event and in the weeks after Deepwater Horizon sank, numerous attempts were made to activate the BOP stack—initiation of the emergency disconnect sequence from the failing rig, automated dead-man circuitry on the BOP stack, even remotely operated vehicles working directly on the stack’s “autoshear” function, one mile down. Nothing stopped the flow of oil.
Even while the oil industry was working to shut down the well and contain the spill, the Departments of Interior and Homeland Security signed an order to begin an investigation. In August, they released a competitive Request for Proposal (RFP) for an analysis of the BOP operation and failure to seal the well. On September 1, DET NORSKE VERITAS (U.S.A.), Inc., Columbus, Ohio, was awarded a contract to determine the performance and possible failure modes of the BOP stack. DNV pulled together an expert team of 40 individuals in forensic investigation, materials specialists, BOP operation, systems controls, and computer modeling from its Columbus, Ohio, Houston, and Høvik, Norway offices to address all issues involved in this multidisciplinary investigation.
The DNV team assembled a base of operations at NASA’s Michoud facility in New Orleans. The intervention vessel Q-4000 raised the BOP stack and delivered it to a temporary enclosure there for investigation.
Finite element analysis as a forensics tool
Shane Finneran, project engineer and team lead in the Computer Aided Engineering (CAE) Group at DNV’s Materials and Corrosion Technology Center, Dublin, Ohio, was a key player in the investigation. His team led the 3D laser scanning and computer modeling initiatives and assisted with materials evaluation and damage assessment.
DNV faced the problem of quickly constructing and testing numerous computer models of the stack’s mechanical components. They turned to Abaqus FEA software (from SIMULIA, an application from Dassault Systèmes’ 3DEXPERIENCE technology), which has been part of DNV’s investigative toolkit for over a decade.
FEA provided DNV with a rapid, accurate methodology to simulate and evaluate the likelihood of proposed scenarios, many of which would have been difficult and impractical to assess with physical testing.
A 200-page report published by DNV for the Department of the Interior’s Bureau of Ocean Energy Management, Regulation, and Enforcement (BOEMRE) explains in great detail the reconstruction process and test methodology used by DNV, as well as their findings.
The BOP stack, together with several pieces of drill pipe, was raised from the well site and transferred to a holding facility at NASA-Michoud. The team cleaned, photographed, and cataloged the stack, disassembling where necessary to get at its inner workings.
Hydraulic fluids and metal samples were taken for analysis, the stack’s control mechanisms and their batteries, actuators, and solenoids were tested, and the casing and blind shear rams, variable bore rams, and upper and lower annular preventers were all visually inspected and 3D laser scanned.
DNV then used the laser scans to construct as-is 3D CAD models of the damaged equipment, especially in the area of the BSR, the blind shear ram, which was the only ram on the BOP designed to cut the drill pipe and seal the well bore.
SolidWorks software, also from Dassault Systèmes, was used to convert the original CAD files of the ram components into simplified surfaces for use with Abaqus FEA, enabling the team to simulate and virtually test their theories of what happened.
What went wrong
Simply put, a drill pipe is a tube within a tube. The outer tube is the bore of the well, and the inner tube the drill pipe, which in turn contains the drill head. As the drill head rotates and moves down within the well bore, pumps aboard the drill platform force a viscous fluid called mud down with it. The mud lubricates and cools the drill head, while simultaneously flushing dirt and cut bits of rock out the bottom into the ring-shaped ‘annulus’ space between the drill pipe and the outside tube, or casing.
The huge BOP stack sits on the sea floor directly above the wellhead. Its two halves together are as tall as a six-story building and weigh over 400 tons. The top half, called a Lower Marine Riser Package (LMRP) contains two electronic control pods together with a pair of donut-shaped sealing devices called the Upper and Lower annular preventers. The preventers seal around the drill pipe and regulate upward fluid flow.
The lower half of the BOP stack contains a series of shear and bore ‘rams,’ and the valves and hydraulics that actuate them. Depending on the circumstances, these rams serve to ‘choke’ the well, or ‘kill’ it if necessary.
Engineers from DET NORSKE VERITAS (U.S.A.), Inc., (DNV) were brought in to determine the performance and possible failure modes of the BOP stack. In their investigation, the team started with a buckling analysis to determine what the necessary load would have been to move the drill pipe to the edge of the casing. The FEA models indicated that the applied pressures would have been sufficient to force it out of position.
From there, the engineering team needed to determine whether the pipe would have sheared had it been in the correct position, and what forces were needed to shear it off-center. Using shear damage parameters, in conjunction with the known elastic and strength values of the material, the FEA data validated the estimated pressures needed to shear the pipe under a center-load condition. The analysis showed that with the pipe off-center, the rams would have been prevented from closing fully. This allowed flow past the blind shear rams and caused significant erosion of the blind shear ram components and wellbore, resulting in failure to seal the pipe.