Oil and gas metering systems
The process of storing and delivering processed fluids to the midstream operator is one of the most relevant in the oil and gas value chain. The amount of product transferred during this stage has to be precisely measured as it implies a transfer of ownership (Custody Transfer Metering).
Metering stations allow operators to monitor and manage the oil and natural gas exported from the production installation. These employ specialized meters to measure the natural gas or oil as it flows through the pipeline, without impeding its movement. Measurement equipment has to be tested and calibrated at regular intervals.
Modern computing technologies and modelling have aided design engineers for the last 20 years. CFD and FEA analyses have helped designers of tanks, meters and offloading equipment to efficiently design and optimise such a sensitive process of the oil and gas production chain.
Liquid metering
Guidelines for liquid hydrocarbon measurement are detailed in the American Petroleum Institute’s (API's) Manual of Petroleum Measurement Standards (MPMS) and manufacturers need to ensure that their products comply with the basic rules of accuracy, linearity and repeatability while also guaranteeing acceptable levels of resolution and turndown.
CFD analysis is extremely powerful for predicting flow behaviour through the different sections of a metering installation. Upstream of the meter it evaluates the influence on the flow stream of strainers, flanged connections, valves, elbows and piping turns and obtains the minimum straight length required for proper measurement on a given installation. Other effects such as erosion, debris impacts or corrosion can be accurately studied using mathematical modelling and computational techniques.
Coupled CFD and FEA methods can be used for determining the sources and spectral composition of unwanted vibrations due to fluid motion (fluid induced vibration) as well as their effects. These vibrations are often induced by the unsteady turbulent flow generated by inline obstacles, the pipeline layout or even the liquid meter components. They can have an effect on the accuracy of meter readings, as well as the risk of fatigue damage and coupled CFD-FEA models are a reliable tool for studying these effects.
Turbine meters, Coriolis meters and positive displacement meters are very different in construction and measurement technology, but all of them share some common challenges. Stress, thermal expansion, fluid velocity changes and debris impacts are just some of the typical challenges that these flowmeters have to cope with in operation.
Designers and operators often rely on CFD and FEA techniques to make sure a new piece of equipment or an in-service installation would work optimally across a range of liquid and thermal conditions.
Other interesting studies in this field relate to the influence of the flow velocities and control valve configurations with regards to flashing and cavitation problems. Inference meters, especially turbine meters may experience cavitation or even liquid flashing depending on the fluid properties and velocity. The configuration of the control valve can be assessed by modelling extreme fluid dynamics scenarios and assessing the possibility of cavitation or flashing.
Gas metering
Gas metering technology evolves quickly. The traditional approaches such as the orifice plates or turbine meters have been steadily replaced by newer technologies, in particular ultrasonic and Coriolis meters. Meter materials, parts, measurement technology and capabilities vary vastly from one meter type to the other. However all technologies have taken advantage of mathematical modelling for concept design, optimisations and failure analysis.
PRE Technologies possess a large experience of gas metering equipment and installation analysis. Using computational technologies such as CFD and FEA and following the relevant international standards, such as ISO Standard 5167 and AGA Standard 3 for orifice meters and ISO Standard 9951 and OIML R32 for turbine meters, we have helped designers and operators minimise risks and costs on their gas metering design and maintenance.
Orifice gas meters rely on the measurement of the pressure drop caused by an orifice plate located across the gas stream. While in essence the technology is quite simple, many operational events may affect the readings. Extreme flow stream conditions may also occur downstream of the orifice (vena contracta). CFD analysis help designers understand and dimension the plate and orifice devices to suit each application. Thermal studies may also be carried out at different gas operating conditions in order to determine the temperatures expected downstream as a result of the orifice.
Turbine meters face completely different technical challenges. A basic turbine meter consists of pressure-containing meter housing with end flanges; a set of internals, incorporating the turbine wheel and gearing mechanisms; and a means of counting the turbine wheel revolutions. Moving parts and gas turbulence may generate unwanted vibration downstream potentially leading to fatigue issues.
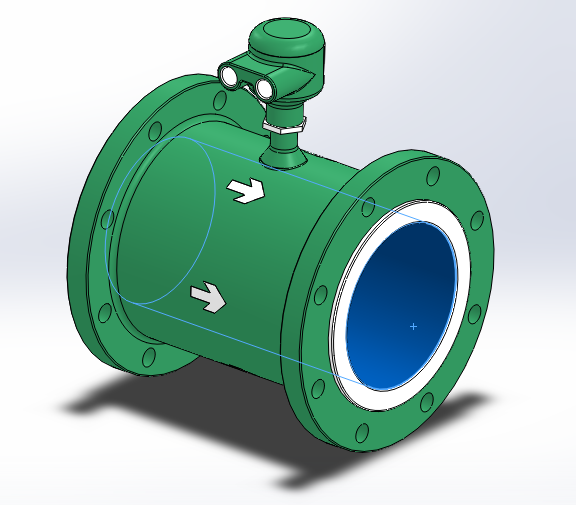
An alternative to the orifice and turbine meter types is the Coriolis meter. The construction and the measurement technology of Coriolis meters is completely different from the more traditional flowmeters, comprising two main parts; a sensor (primary element) and a transmitter (secondary element). In this case the U- tube vibration and twisting and the sensing coil oscillation frequency can be predicted using mathematical modelling, helping the designers to optimise these components. Stress calculations and fatigue life are typical studies delivered to designers and operators of this type of gas meters.
Recent technical progress has made the multipath transit time ultrasonic meter (USM) a reliable alternative to turbine and orifice gas meters. The complex design of the meter body and the transducer pairs can be aided by proper CFD modelling for the fluid motion and FEA modelling for mechanical performance evaluations.
For more information on other services for processing systems, please go to the processing services tab or contact us here.
Our services for this sector
Liquid metering
- Stress and fatigue calculations on liquid meters for relevant Standards
- Upstream configuration influence on liquid metering (turns, elbows, valves)
- Flashing and cavitation prediction (CFD analysis)
- Fluid induced vibration analysis on liquid meters
Gas metering
- Stress and fatigue calculations on gas meters for relevant Standards
- Upstream configuration influence on liquid metering (turns, elbows, valves)
- Orifice and turbine meters mechanical assessment
- Fluid induced vibration analysis on gas meters
Multi-phase metering
- Multi-phase CFD analysis on a variety of produce compositions
- Stress and fatigue calculations on multi-phase meters for relevant Standards
- Upstream configuration influence on multi-phase metering (turns, elbows, valves)
- Fluid induced vibration analysis on multi-phase meters