Rig stability and mooring
Meteorological conditions in the North Sea can be extremely harsh and unpredictable. Keeping floating equipment in position, during drilling operations or production, is a challenging engineering task.
Submerged equipment also need to withstand variable sea wave and current conditions during their operating life.
The dynamic loading due to waves, tides, current and wind therefore need to be carefully considered when selecting and designing offshore-based systems. The same criteria apply to offshore installation activities. Subsea pipelines, valves and manifolds deployment has to be thoroughly planned according to expected and extreme sea conditions.
Rig stability
Semisubmersible structures are often used for ultra-deep water drilling purposes due to their stability on harsh waters. Lately the same structures have been used for production and processing too. Hull and structure designs are constantly optimised. CFD and FEA models help designers evaluate the stability of the structure under different sea and wind conditions and also for different tanks payloads.
Centre of gravity, centre of buoyancy and mooring configuration play a vital role on these stability calculations. Sea and wind conditions are input to these models often obtained using historical data for the geographical area (metocean). Drilling operations are the most demanding in terms of stability. While drill strings and drilling mud risers are somewhat flexible, MODUs need to keep their relative position to the wellbore accurately and rolling/pitching need to be avoided.
Spars and tension leg platforms have been regularly used for offshore production and processing. Positioning and stability requirements are less demanding than in drilling facilities. However production and processing efficiency can be severely affected on a poorly moored platform. Sloshing effects on oil processing equipment may reduce separation rates and therefore compromise the overall process productivity. Besides, dynamical forces causing oscillating stresses on structures and equipment can cause fatigue issues that may ultimately lead to equipment failure. Spars and tension leg platform dynamics can be studied for a variety of meteorological conditions and determine the best mooring and payload configurations. PRE Technologies possess experience on modelling these dynamic effects on production platforms to determine both the expected movement and also the subsequent stress and fatigue on the structures.

The main advantage of Floating Production, Storage and Offloading (FPSO) vessels is that they are standalone structures that do not need external infrastructure such as pipelines or storage. Typically a tanker type hull or barge converted from an existing crude oil tanker (VLCC or ULCC), these vessels operate differently from semisubs and spars. The wellheads or subsea risers from the sea bottom are located on a bow-mounted turret so that the ship can rotate freely to point into wind, waves or current. The turret has wire rope and chain connections to several anchors (POSMOOR) or it can be dynamically positioned using thrusters (DYNPOS). Massive dynamic loads of wind, waves and currents are applied continuously into that rotational structure which needs to keep its position in order avoid damage on production risers. FEA modelling has been intensely used for the design of the pivotal turret and mooring systems using as inputs the dynamical loads and displacements calculated using stability CFD calculations.
Loading on tankers involves loading arms and jetties, pumps and valves as well as sophisticated single point mooring systems that allow the tanker to dock and load the product even in bad weather. Tanker loading systems are complex, both because of the volume involved, and because several loading arms will normally interact with the tanker's ballast system to control the loading operation. The tanks must be filled in a certain sequence, otherwise the tanker's structure might be damaged due to uneven stresses. Loading/unloading sequences can be simulated using CFD and FEA coupled methods. Stability calculations as well as structural stresses on the hull can be predicted using this approach.
Mooring
There are several mooring patterns very extended for offshore rigs and vessels operating on the North Sea. These configurations are selected according to the shape of the vessel being moored and the sea conditions in which it will be moored. Mooring line materials are often selected following Standard guidelines and experience. Lines are typically made up of synthetic fibre rope, wire, chain (ORQ and RQ4) or a combination of the three.
While CFD stability studies are regularly used for overall structure dynamics, FEA models can also be applied to optimise the mechanical performance of localised features. Pile and foundation strength, mooring line connections and tendon attachments to the seabed are often subject to stress and fatigue analyses. Linear elastic models provide insightful data of maximum stress expected under peak loading. Non-linear dynamic models, on the other hand, provide the mechanical response of the system to dynamical time-varying forces. PRE Technologies has a large background of analysis and optimisation of connections, fixations and joints relating to mooring systems.
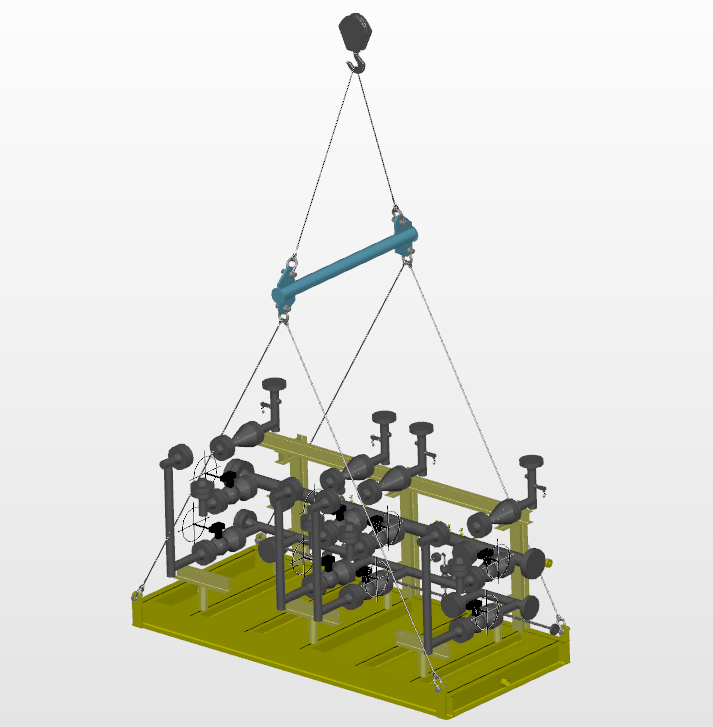
Deployment
With major drilling and production facilities located offshore, the oil and gas industry must rely on an efficient and safe way to deploy and install this equipment. The sector has developed innovative ways to overcome heavy lift challenges offshore, including lift barges and floatover devices. Modular and integral lifts, surface or subsea deployments need thorough planning and analysis. Computational tools and specific software is normally used to dimension and plan subsea equipment deployment. PRE Technologies can help you design your installation operations, define lifting equipment requirements, predict operational issues due to marine conditions and analyse the dynamics involved on the deployment process.
For more information on other services for offshore rigs and platforms, please go to the oil and gas rig tab or contact us here.
Our services for this sector
Rig stability
- Ballast, centre of gravity and centre of buoyancy calculations
- Sea and wind loading (metocean) for stability simulation
- Wave dynamic loading modelling
- Skid and processing equipment sea fastening assessment
Mooring
- Mooring lines configuration assessment
- Stress and fatigue analysis of mooring lines, connections and tendon attachments
- Pile and foundation mechanical assessment
- Non-linear dynamic FEA models for mooring systems
Deployment and installation
- Lift operations dimensioning and stability studies
- Subsea equipment deployment studies
- Offshore rig module and skid deployment analysis
- Sea fastening and module fixings FEA stress analysis