Subsea and downhole processing
While subsea developments have been made possible by technologies such as subsea trees, risers and ROVs, subsea processing has been an elusive solution for many years. Process facilities can now be placed literally anywhere between the reservoir and the product pipeline, including subsea and downhole. Whether describing separation, re-injection or boosting, the advent of subsea and downhole processing is changing the layout of modern offshore developments.

Subsea processing
Subsea processing was developed as a way to minimise surface equipment size and weight and reduce costs of developing deep-water fields. It can encompass some of the following processes: water removal and re-injection or disposal, single-phase and multi-phase boosting of well fluids, sand and solid separation, gas/liquid separation and gas treatment and compression.
It all starts when the produced fluids pass through the wellhead structure. Subsea wellheads are firmly attached to a seabed template and normally consist of a casing head, the tubing head and the valve array or “Christmas tree”. Subsea Christmas trees are designed to withstand extremely large operating pressures (up to 1,400 bar) but also need to be prepared for external loads such as the hydrostatic pressure, current loads or ROV induced loads. CFD analysis has been used over the last 15 years to aid Christmas tree valve designers. Fluid dynamics studies, pressure drop calculations, thermal analysis are just a few examples. On wells where the production fluid is predominantly gas, hydrate formation must be prevented.
CFD can also be used to assess the effectiveness of a variety of hydrate prevention strategies such as insulation of flowmeter, x-mas trees and manifolds, as well as the injection of hydrate formation inhibitors. Effects such as Joule-Thomson cooling on the choke can also be simulated using computational modelling (see our Joule-Thomson cooling example here) and the potential damage due to the cryogenic temperatures downstream of the choke assessed.
FEA models have been widely used on wellhead structural studies as well. Structural integrity under operating or test conditions must be ensured and assessed using relevant Standards, such as ASME VIII Div 2 or API 6 and 17. Pressure loading, external loading from connected assemblies and thermal-mechanical loading can be combined on FEA models of full assemblies according to ASME guidelines in order to assess the risk of plastic collapse. Additionally, more advanced studies on subsea components, such as dropped object impact analysis, can be performed using dynamic FEA modelling.
One of the most common subsea processing applications is the production fluid boosting. On deepwater or ultra-deepwater fields, subsea boosting is needed to negate backpressure that is applied to the wells, providing sufficient fluid pressure to lift the production fluid from the reservoir to the sea surface, over what could sometimes be thousands of feet above. CFD studies are used to dimension the pumping needs and also to design the thermal insulation on flow lines and risers to prevent the formation of hydrates or natural gas condensates.
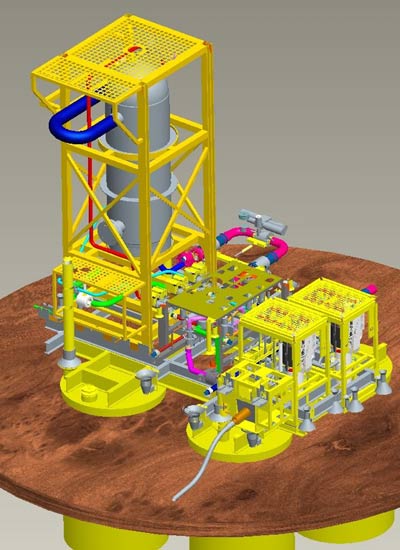
Gas/liquid separation can also be achieved in subsea environments. Unlike surface processing, where size does not impose a prohibitive cost penalty, seabed installation and intervention require more compact, light and reliable solutions if they are to be viable. For vessels designed for deep water, the key design criterion is often the external collapse pressure at depth. Based on ASME VIII pressure codes, vessel walls can be quite thick, causing even small-diameter vessels to be relatively heavy. The use of high-strength steel and stiffening rings may help reduce vessel wall thickness thus reducing system weight and cost.
New vessel geometries, materials and reinforcement features can be quickly evaluated using FEA linear elastic analysis. The risk of plastic collapse of the structure can then be predicted and the geometry optimised accordingly in a reliable and in-expensive manner. Likewise processing and separation performance can be estimated using CFD models (see oil processing tab for more information).
Remotely Operated Vehicles, or ROVs, have become an integral part of deep-water developments. ROVs are connected to the surface structures via an umbilical link that houses communications cables, an energy source and information/control cables. ROV operations range from changing the wellhead sealing gaskets or control/inspection of hardware, to more heavy duty operations such as aiding drilling activities,
installing risers/umbilicals, moving production skids and even deploying subsea templates.
PRE Technologies can help you in the design, planning and risk management of most ROV operations; from deployment and payload studies to stress and impact analyses on the subsea processing equipment due to the ROV operation. FEA and kinematic studies have also been applied to the design of specific tools for unconventional subsea ROV activities.
Downhole processing
In order to debottleneck surface facilities many processes normally employed on the surface may be adapted to downhole conditions. Typical examples are pumping, phase separation and compression. Gas/liquid separation, oil/water separation, water injection and gas injection are possible with these technologies however separation efficiency is poorer than on surface separators.
Performance tests on these processes are practically impossible due to the difficult access and confined working area. That is why CFD and FEA modelling techniques are so useful in providing realistic insights into the feasibility and expected efficiency of a certain processing stage located downhole. Multi-phase modelling of separators and fluid dynamics studies on reinjection systems are commonly performed.

Another important activity carried out during production is artificial lifting. This is normally achieved using gas lift or an electrical submerged pump (ESP). CFD analysis is crucial in determining the best approach for each particular case. Multi-phase CFD models including gas bubble dynamics and liquid multi-phase interactions can be used to determine the requirements of the gas lift system in terms of gas volume and release pressure setting for the injection valves.
Well stimulation is performed to commence production from the reservoir or to further encourage flow from an already existing well that has become under-productive. Chemical injection, acid treatment, steam heating and fracturing techniques are often used. CFD and FEA coupled methodology helps operators determine the efficiency of steam heating or pressure wave based techniques such as explosive or hydraulic fracturing on damage removal for a specific reservoir.
For more information on other services for subsea systems, please go to the subsea services tab or contact us here.
Our services for this sector
Subsea processing
- Subsea wellhead thermal FEA and CFD calculations
- Stress, vibrational and fatigue studies on valves, connections and pipelines
- ASME and API compliance assessments for subsea separators
- Joule-Thomson cooling and hydrate formation calculations
- CFD analysis for boosting on different thermal/pressure conditions
Downhole processing
- CFD analysis for artificial lifting operations
- Reinjection operations risk assessment and fluid-dynamics
- ASME and API compliance assessments for downhole separators
- Mechanical and fluid dynamics analysis for different well stimulation techniques
- Well intervention operations risk assessment
ROV operations
- Stress, vibrational and fatigue studies for ROV structures and actuators
- CFD analysis of ROV dynamics
- ROV's operations risk assessment and impact on valves and structures
- Design of task-specific tools and actuators for ROVs