Gas processing
A gas processing facility encompasses the equipment between the gas wells and the export pipeline or other transportation method where the gas needs to meet the sales requirements of the purchaser. This process normally starts in a separator vessel where wet gas is directed to a glycol dehydrator where most of the liquid content is removed.
Downstream of the dehydrator a number of heat exchangers, a series of compressors and finally a sweetening process to remove corrosive components are typically used.
The full process is often designed for the specific requirements of the operator and requires an experienced process engineer to dimension it according to the expected product composition. CFD and FEA technologies can help process designers in this endeavour. Thermal and fluid dynamics studies will help determining the process efficiency of various designs and hence affect the equipment dimensioning. Stress, vibration and fatigue analyses will help assess the likelihood of failures during operation. Corrosion and erosion on the various sections of the system can also be modelled aiding the maintenance scheduling during operation or the extension of plant life through design modifications and retrofitting.
Gas dehydration

A key process on any offshore gas treatment facility is the liquid content removal. Water is often removed from gas with a glycol dehydration system but other dehydration processes such as those based on solid-desiccant adsorption, refrigeration and membrane permeation have been recently used too.
Glycol dehydration systems are commonly tailored for the specific requirements of the oil and gas field. Process engineers regularly rely on mathematical models to dimension the main areas of the dehydrator. The glycol contactor or absorber is certainly one stage where fluid dynamics simulations can be applied. The contact area configuration, whether it contain trays, random packing, or structured packing can be optimised using multi-phase CFD modelling. The sensitivity of the separation process to aspects such as; bubble size distribution, flow rates and glycol hygroscopy, which have an effect on the dehydration process can be determined using CFD models.
The rich glycol exiting the bottom of the tower is regenerated in a continuous process. First, the rich glycol goes to a separator to remove any condensed hydrocarbons, and then it is preheated and filtered before being sent to a reboiler or regenerator.
The regeneration is a complex process involving circulation through a still column, a heat exchanger, a flash tank, a filter and a reboiler vessel. Heat transfer analysis, pressure drop calculations and thermal fatigue prediction are some of the most common studies for this stage in the process. Additionally, flow and thermal studies of the lean/rich glycol heat exchanger are often required and help the selection and dimensioning of the equipment.
Gas compression
Designing a gas compression process requires a multi-disciplinary team with years of experience and a profound understanding of the required gas properties and operating conditions at the upstream end-use stage.
Gas flow rate, pressure differential, load management, power requirement and choke flow are just some of the factors the process engineers have to consider. Fluid dynamics simulation can be used to model the expected operational conditions up and downstream of the compressor and assess the system design and balance prior to detailed plant design.
Several types of compressors are used for gas compression, normally characterised by their operating power, speed, pressure and volume. Reciprocating, screw, axial blade and centrifugal compressors are largely used on any gas processing facility, either on or offshore. PRE Technologies has a strong background on analysis and design support for a number of compression devices using modelling techniques to predict stress, vibrations and fatigue performance on different elements of the compressor. Integral and separable configurations evaluation and vibration transmission to surrounding structures, frames and skids are also part of the capabilities portfolio of PRE Technologies.
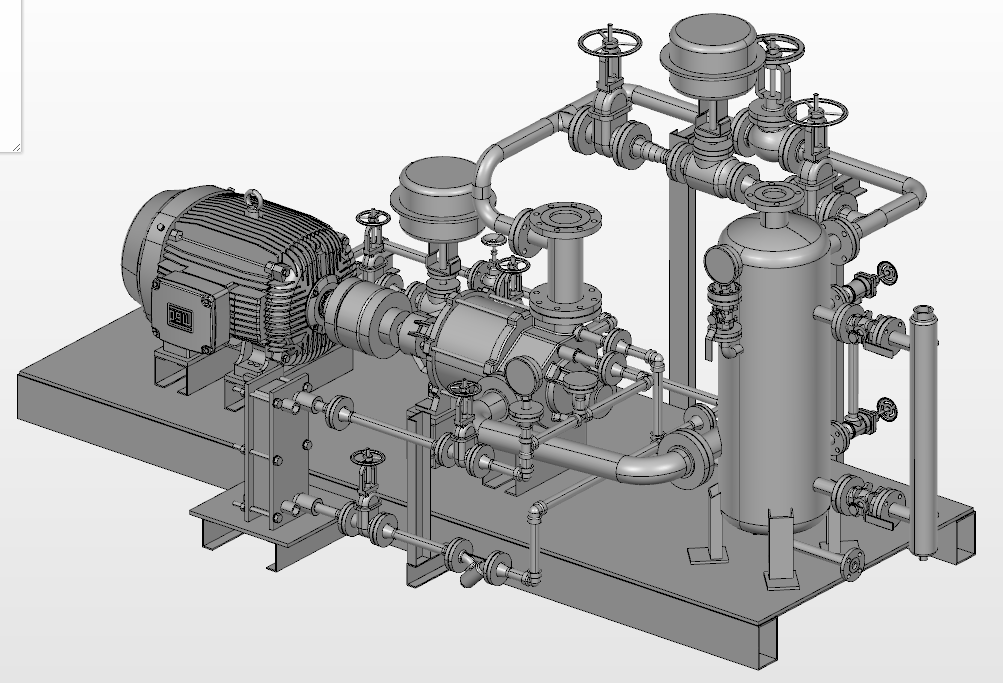
Compressor selection depends on the required operational conditions and these depend largely on the final application of the compressed gas. Re-compression of flashed gas, gas lift pumping, well reinjection and pipeline boosting are the most typical applications. PRE Technologies has experience on a variety of technologies involving different study scopes, from small elements optimisation to full compression system assessments. These wider scope analyses often include upstream and downstream equipment, valves and pipelines into the modelling to have a broader view on the gas interactions across the full process.
Gas heating and cooling
Produced gas pressure and temperature varies not only from well to well but also during the reservoir lifetime. Two opposite problems may arise from these changing conditions that require pressure and thermal conditioning of the gas produced.
If the pressure is too high it must be reduced to the appropriate pipeline pressure, often through an expansion valve or choke. In this constant enthalpy process (Joule-Thomson cooling), as the gas pressure is reduced, the gas cools rapidly, reaching cryogenic temperatures in which gas temperatures can fall below the hydrate formation temperature.
These hydrates can plug the choke and flowline. To avoid this, high-pressure gas wells usually require a line heater that encloses the flowline and choke inside a hot water bath to keep the well fluids above the hydrate formation temperature. Please read PRE’s white paper on wellhead choke thermal analysis and Joule-Thomson cooling which can be found here.
Heat exchangers of various forms are used to cool the gas. PRE Technologies has a large background in assisting designers and operators with optimisation studies and failure analyses. Plate heat exchangers and tube and shell exchangers require extensive analysis prior to any manufacturing activity. Flow and thermal performance analysis on a variety of media and stream conditions together with proper mechanical assessment (pressure and thermal stress and oscillating loading fatigue) are typically carried out for all new designs.
For more information on other services for processing systems, please go to the processing services tab or contact us here.
Our services for this sector
Gas dehydration
- Scrubber thermal and mechanical FEA calculations
- Fluid dynamical assessment on dehydrator contactor areas
- Regenerator and reboiler thermal stress and fatigue calculations
- ASME and API compliance assessments for scrubber and reboiler vessels
Gas compression
- Compressor skid stress, vibrations and fatigue analyses
- Compressor part mechanical optimisation
- Gas compression system fluid dynamics optimisation
- Thermal and stress analyses on compression system pipelines
- VIV studies for vibration prevention downstream of the compressor
Gas heating and cooling
- ASME and API compliance assessments for plate and tube-and-shell HE
- Joule-Thomson cooling calculations using CFD
- Stress, vibrational and fatigue studies for heat exchangers
- Thermal performance optimisation of heat exchangers