Automotive - Plastics manufacturing
By volume, more plastics than steel are used in today's cars. Plastics’ versatility aids the automotive industry in meeting ever more stringent requirements in terms of economical performance, safety, comfort and environmental considerations. Plastics also play a key role in providing cost effective buses and trucks for transporting people and goods efficiently. However, automotive industry is well known for its demanding requirements.

Plastic components need to be durable and strong, versatile, light-weight, aesthetically pleasant and their assembly easy and repeatable. Simulation is of paramount importance when trying to meet all these requirements. Mechanical and vibrational performance, as well as creeping analysis are just a few of the studies that PRE Technologies can perform.
The average new car in 1980 contained 8% plastics by weight. A similar car today contains around 11%. The increased use of plastics reduces the weight of vehicles and consequently emissions. Using one kilogram of plastics in a car can replace between two and three kilograms of traditional materials which over the average lifespan of a vehicle will reduce fuel consumption by 750 litres.
This constitutes a huge opportunity but the industry has to deliver. Plastic component manufacturers have to stay in the vanguard of innovation and the only way to do so is to take advantage of technologies such as simulation and mathematical modelling.
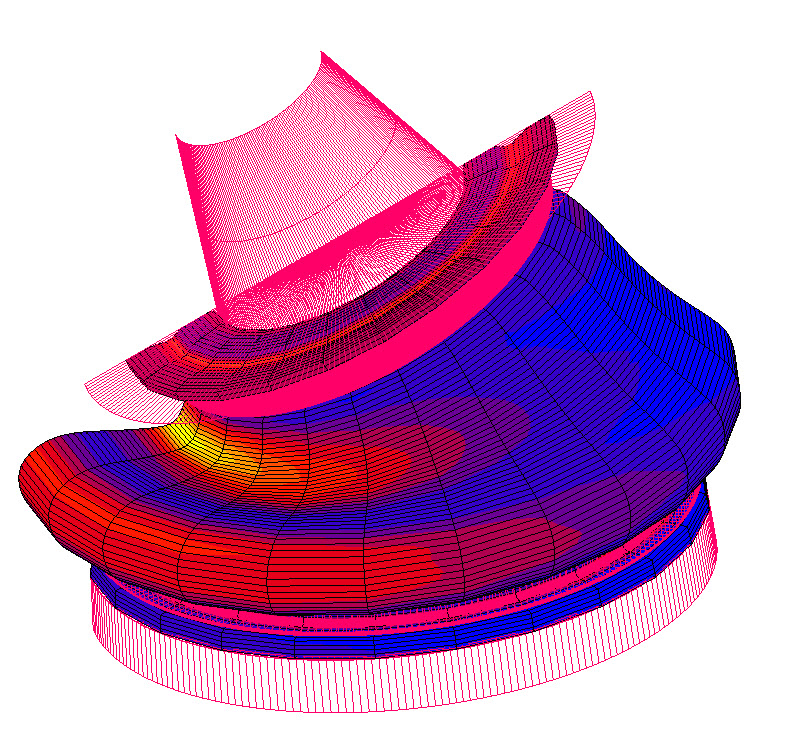
The automotive sector is very dynamic in terms of research, development and innovation. Automotive manufacturers are always looking for ways to reduce weight and improve efficiency and plastics provide great opportunities to reach these goals.
In the future carbon-fibre is likely to play an important role in replacing traditional materials and could potentially reduce the weight of cars by a half replacing traditional materials.Composite simulation is one of PRE Technologies’ areas of expertise and has a huge room for development and commercial expansion.
For more information on other services for the plastic manufacturing sector, please go to the plastic manufacturing services tab.
For more information on other services for the automotive sector, please go to the automotive metal services tab.
Our services for this sector
Components design:
- Stress and vibrational studies of external injection moulded parts (fenders, bumpers, mirror gaskets, etc)
- Thermal and mechanical studies of electronic components and cases
- Rubbers deformation analysis
- Seat foam comfort and ergonomics viscoelastic study
- Mechanical performance study of rubber joints
- Lighting thermal CFD analysis
- Interior injection moulded and compression moulded parts design and analysis
- Thermo-stress viscoelastic deformations (creeping)
Components manufacture:
- Injection moulding mould filling simulation
- Compression moulding process optimisation
- Rotomoulding process cycle calculations
- Injection moulding thermal optimisation