Plastic manufacturing
The plastics industry has a long and complex supply chain stretching from the producers of plastics raw materials and additives to the end-user (customer industries). Different product groups, for example automotive components and retail packaging, have markedly different supply chains. Different sources of organic renewable resins as well as composites and technical additives are being developed as a response to the market demands of environmentally friendly, mechanically performing and cheap plastic products.
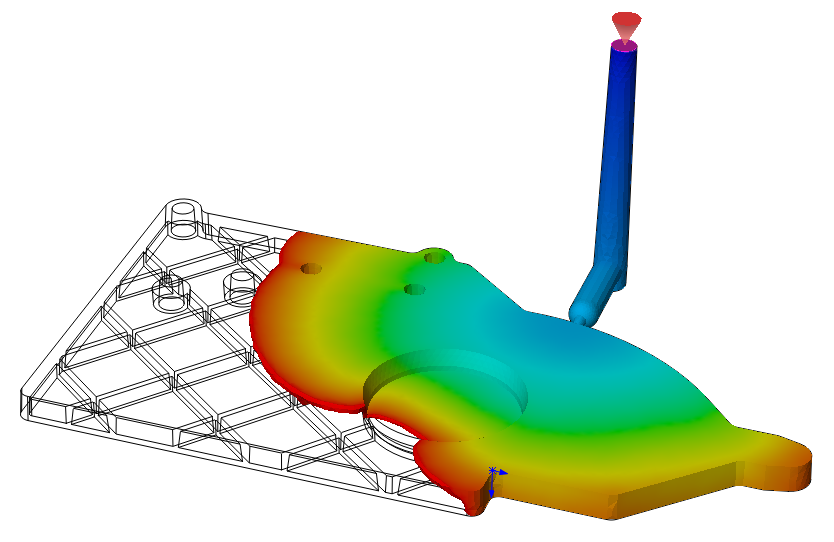
The sector is extremely wide,covering raw material production of hundreds of different natural and synthetic resins, product design for a wide variety of different sectors and product manufacturing using tens of different technologies. In this scenario simulation and mathematical modelling play a relevant role. It helps designers understand their product’s mechanical and thermal performance early in the design stage, saving lots of time and money otherwise spent in expensive dies and moulds. It also helps manufacturers in their attempt to optimise their processes in aspects such as mould flow filling, heating and cooling process efficiencies and quality of the finished part.
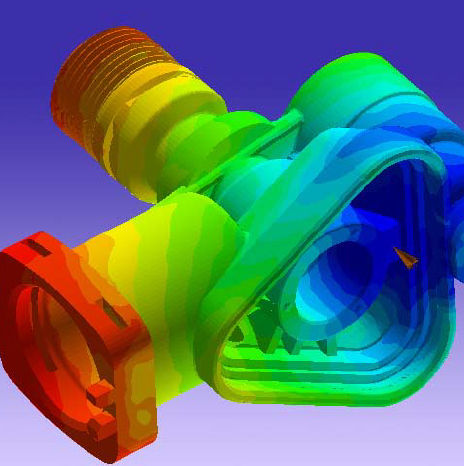
Thermoplastic and thermosetting plastics differ completely not only in their chemical structure, but also in the way they are manufactured and the applications they are used for.
Common thermoplastic manufacturing techniques include injection moulding, extrusion, blow moulding, rotomoulding, machining or combinations of two or more of those technologies. All of them rely on thermal processes to melt the plastic and cool it down and also geometrical and mechanical restrictions to give the finished part the desired shape. Some of them also include the use of specific additives, pressurized gases or liquids as well as non-conventional sources of energy such as electromagnetic induction and ultrasounds. Simulation provides extremely valuable information to better understand these processes, where and how they may fail and also optimise them in terms of cycle time and energy consumption.
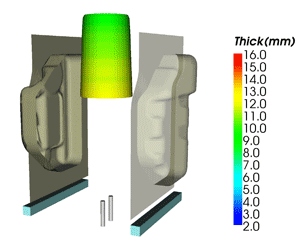
For thermosetting plastics, most common manufacturing techniques are injection and reaction injection moulding, compression moulding, pultrusion and resin transfer moulding. Processes differ from thermoplastic manufacturing insofar some thermosets are liquid at room temperature, other need two phases (catalyst and resin) to be mixed in the moulds or require higher pressures and temperatures to be cured. CFD models of mould flow filling, FEA or CFD thermal models of the curing processes and mechanical performance of the moulds under high pressure conditions are just some of the most typical simulations.
News
Virtual testing of composites: Beyond make & break
Thursday, December 26, 2013
Beyond the obvious lightweighting advantages, the thing that makes composites so appealing to the aerospace market is the variability that permits …
The Role of Computational Fluid Dynamics in Process Industries
Friday, January 17, 2014
Computational fluid dynamics has enormous potential for industry in the twenty-first century.
Automotive
By volume, more plastics than steel are used in today's cars. Plastics’ versatility aids the automotive industry in meeting ever more stringent requirements in terms of economical performance, safety, comfort and environmental considerations.
Read moreAeronautics
From aircraft and missiles to satellites and space shuttles, plastic components and products have been essential enablers of the most significant developments in civilian air travel, military air power and space exploration.
Read more