Biofuel power
Feedstocks do not develop at sufficient yield, land is not available and affordable, processing technologies fail to achieve the required levels of efficiency, from front end processing to final-step fuel finishing, or policies and finance do not support the sector.
These are just a few of the main issues the biofuel industry faces these days. New technologies are developed every day trying to achieve that extra yield in a stage of the process that would make it profitable and less dependent on subsidies. Evaluation of novel feedstocks, new chemical and thermal processes, optimisation of oxygen removal and supply chain redesign are just a few of the sector’s responses to these issues.Feedstocks do not develop at sufficient yield, land is not available and affordable, processing technologies fail to achieve the required levels of efficiency, from front end processing to final-step fuel finishing, or policies and finance do not support the sector. These are just a few of the main issues the biofuel indu stry faces these days.
New technologies are developed every day trying to achieve that extra yield in a stage of the process that would make it profitable and less dependent on subsidies. Evaluation of novel feedstocks, new chemical and thermal processes, optimisation of oxygen removal and supply chain redesign are just a few of the sector’s responses to these issues.
Whether your plant produces biodiesel from animal fats or algae’s oil or biogas from manure or sewage waste, simulation tools can help you optimise the different stages in the process by generating and evaluating virtual prototypes. These virtual prototypes will provide you with a detailed insight of you process efficiency in terms of mechanical, thermal, fluid dynamic and chemical performance.
PRE Technologies has very relevant experience in CFD analysis of different biofuel production stages where processes were optimised early in the design stage, as well as FEA simulations where tanks, valves, heat exchangers and mixers were calculated in order to obtain their mechanical and vibrational performance limits.
We follow standards and design guidelines of the UK environment agency, OFGEM and the department for environment, food and rural affairs. We want to make sure our delivered solution will be implementable at an industrial scale complying with all regulations.
Biodiesel
A wide variety of vegetable and animal fats or oils are used to produce biodiesel. A number of thermal and chemical processes are used as well to promote esterification and transesterification. Finally, different batch or continuous processes are used to separate by-products such as glycerol and methanol to obtain further diesel purity. All these different factors make the biodiesel production a very complex process and make every biodiesel plant different in its needs and technical challenges.

On the feedstock pre-treatment stage, mechanical filtration and separation can be evaluated using CFD analysis. Flow analysis to avoid stagnation areas and filter fouling can be performed, as well as water content removal studies.
From simple batch process reactions using catalysts to more advanced continuous processes such as fixed-bed, ultra-high shear, supercritical or ultrasonic reactions, simulation and mathematical modelling can provide critical reactor design information. This studies range from equipment vibrational/ fatigue performance and thermal/ chemical process efficiency to flow analysis of the different liquid phases.
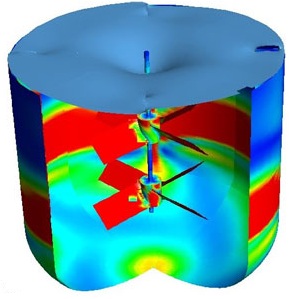
Finally on the purification stage,the different by-products are separated and the techniques used and order of separation is process-dependent.Again simulation is very adequate to aid this stage’s design.Multi-phase CFD models provide very useful information on the mixing/separation performance and can help you optimise your equipment design to make thermal and chemical reactions quicker and more efficient.
Biogas
Biogas is mostly produced as landfill gas (LFG) or digested gas. However there is a large variety of processes, such as meso and thermofilic digestions according to the feedstock used as well as the type of final and by-products to obtain. No matter the technology used, mechanical, thermal and fluid dynamical simulations can speed up the design process and help you find the root causes of the failures during operation.
For the pre-treatment processes such as screening, maceration and pasteurisation, PRE Technologies can provide simulation services ranging from stress and vibrational analysis of maceration equipment to fluid dynamical analysis of the different pasteurisation processes to identify potential improvements in terms of efficiency and reliability.

Digesters vary significantly depending on the feedstocks used, the process (thermo or mesophilic) and the final products to obtain. Mixing, temperature homogeneity and equipment air tightness are of paramount importance. Again, fluid dynamic analysis can be used to understand the process parameters and make sure mixing, temperature and fermentation are optimised to get the maximum process yield.
Gas and liquid multiphase models can be used to determine the best tank geometries, mechanical agitators and thermal conditions even before the detailed plant design has started. Digestate treatments and biomethane purification processes can be studied using CFD models too.
For more information on other services for the energy sector, please go to the renewable energy services tab or contact us here.
Our services for this sector
Biodiesel technology
- Pre-treatment fluid dynamic model for filtration/separation
- Reactor efficiency for different thermal and chemical conditions
- Stress, vibrational and fatigue performance of pipes, valves and pressurised reservoirs
- Thermal/studies of valves and other fluid equipment
- Thermal/studies of different reactor technologies
Biogas technology
- Stress, vibrational and fatigue performance of maceration equipment
- Thermal and fluid simulations of pasteurisation processes
- Digester fluid, thermal and chemical optimisation
- Stress, vibrational and fatigue performance of pipes, valves and pressurised reservoirs
- CFD model for digester tank geometry and agitators optimisation
- Gas separation and purification using multi-phase diffusion CFD models