Stress and fatigue modelling white paper
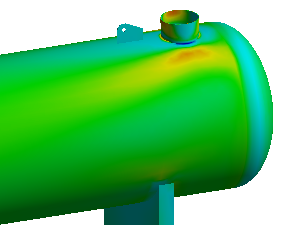
Structural assessment is one of the major engineering issues and its difficulty lays in the inherently uncertain and complex prediction of metallic materials' failure or mechanical limits for a structure under cycling loading. PRE Technologies can play a vital role in mitigating risk due to their experience in structural calculations supported by CFD and FEA for the oil and gas sector. We have conducted analyses for different assembly parts ranging from piping sections subjected to thermal cycling or fluid induced vibration to pressure vessels under oscillating pressure and thermal loads.
In the past engineers studying vessel and piping performance have developed a set of rules based on experience and testing. They discovered that different types and location of stresses do not have the same safety implications or impact on the equipment performance. Their results have led to the empiric discovery that localized stresses around nozzles due to geometric stress risers and membrane or bending stresses do not have the same relevance as they did not led to the same risk of failure. All this knowledge was condensed in the Codes and Standards that now serve as design guidelines for the calculations involved in the design process.
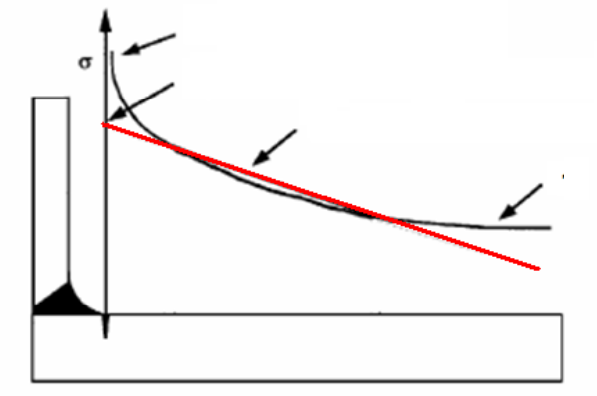
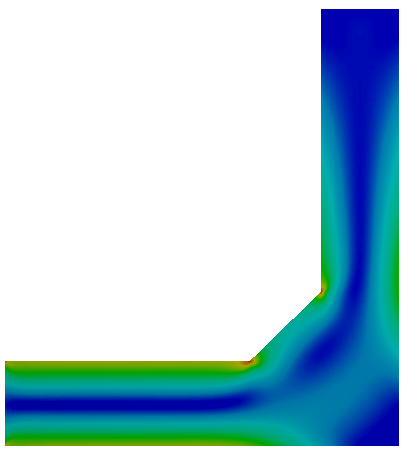
These standards provide a clear methodology to conduct different stress calculations including fatigue failure prediction. ASME VIII-2, BS-5500, EN-13445 and DNV-RP-C203 are widely used for these purposes. The main difference between them lays on the type of stress used for the fatigue calculation; common stress definitions include nominal, notch, structural and hot spot stresses.
This classification of stress sometimes involves a simplification of the six component stress tensors and it is called stress linearization through stress classification lines (SCL). These methods get over the complexity of the stress tensors transforming it to a three-component tensor: Membrane, bending and peak stresses. Adding certain criteria depending on the stress region subject to calculation will lead to a straight forward pass/fail result ultimately enabling the prediction of structural failure and even complex effects as crack propagation. Standards and Codes also provide the input needed to post-process the stress distribution calculated by the FEA method.
PRE Technologies are well known for their ability to perform intelligent engineering and for following the Codes and Standards. We make FEA and CFD modelling rigorous and reliable providing our customers the most advanced simulation services and enabling them to reduce undesirable premature failure of products and processes.
Keep your curiosity in good shape.
For more information on this or any other technical white paper, please contact us.