Aeronautics - Metal manufacturing
In aircraft manufacturing industry, structures must be designed with care because human life often depends on their performance. Structures are subject to one-way and oscillating stresses, the latter giving rise to fatigue. Metal structures are subject to corrosion, and some kinds of corrosion are accelerated in the presence of stress. Aircraft structures are designed with particular attention to weight, for obvious reasons. All these factors constitute a complex framework for designers and manufacturers. That is why this sector is at the vanguard of new materials application and new manufacturing techniques development.
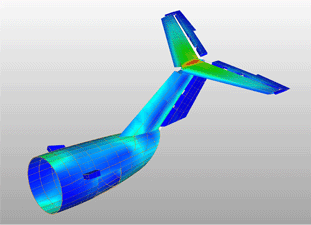
Multi-material structures using ultra-light composites and aluminium alloys are assembled using tens or even hundreds of thousands of fasteners and rivets on every airplane. The work is tiring and noisy, and is one of the main cost components of aircraft manufacture. A good deal of thought has been spent trying to reduce this cost and speed up this phase of aircraft manufacturing.
Fuselage design and manufacturing is one of the most difficult tasks of an aircraft production. Special care is put on light weight,strength,stiffness,manufacturability and cost. Minimising drag while generating a certain uplift is complicated while also focus is put in passengers comfort and ground operations. Joint assessment, stress, fatigue ,vibrational analysis and aerodynamics are some of the typical simulation studies performed over this part of the aircraft.
Likewise wing design must fulfil very demanding requirements. Again strength and stiffness must be combined in this case with flexibility and good vibrational performance. Also flight control devices such as flaps and slaps must share the space with the fuel tanks and the structural parts, such as ribs, stringers, root and spar as well as the engine support, in some cases. Drag and lift CFD analyses are the most obvious examples of simulation studies of a wing, but also modal analysis, fatigue, stress and some dynamic analysis are usually performed.
Very similar analyses are performed over the empennage: vertical and horizontal stabilisers as well as rudder and elevators are susceptible of complex fluid dynamics and mechanical simulations.

Finally, jet engines are very dependent on CFD and FEA analysis for their design and for some stages of their manufacture.
Turbofans, turbojet, pulsejet and also ramjet are technologies in continuous evolution and innovation is often led by a large amount of modelling and simulation.
For more information on other services for the metal manufacturing sector, please go to the metal manufacturing services tab.
For more information on other services for the aeronautics sector,please go to the aeronautics plastic services tab.
Our services for this sector
Fuselage structures:
- Stress,fatigue and vibrational studies of fuselage external cover and ribs
- Aerodynamic study to optimise drag and lift performance of the fuselage
- Fastener and rivet joint reliability and fatigue
- Structures impact studies (large plastic deformations)
- Nose and main landing gear mechanical optimisation
Wing and empennage structures:
- Aerodynamic study to optimise drag and lift performance of wings and empennage stabilisers
- Aerodynamic study to optimise performance of flaps, slaps, rudder and elevators
- Stress, fatigue and vibrational studies of the wing structure: ribs, stringers, root and spar.
- Modal analysis of a wing under different fuel loads
Propulsion engines:
- Stress, fatigue and vibrational studies of jet engine components
- Aerodynamic study to optimise performance of jet's nozzle and mixer
- Thermal CFD for jet's compressor and combustor
- Stress,fatigue and vibrational studies of engine supports and connection to wings or fuselag